1. Test teoretyczny i analiza
Z 3zawory oponowepróbki dostarczone przez firmę, 2 to zawory, a 1 to zawór, który jeszcze nie był używany. W przypadku A i B zawór, który nie był używany, jest oznaczony na szaro. Rysunek 1. Zewnętrzna powierzchnia zaworu A jest płytka, zewnętrzna powierzchnia zaworu B to powierzchnia, zewnętrzna powierzchnia zaworu C to powierzchnia, a zewnętrzna powierzchnia zaworu C to powierzchnia. Zawory A i B są pokryte produktami korozji. Zawory A i B są pęknięte na zagięciach, zewnętrzna część zagięcia jest wzdłuż zaworu, otwór pierścienia zaworu B jest pęknięty w kierunku końca, a biała strzałka między pękniętymi powierzchniami na powierzchni zaworu A jest oznaczona. Z powyższego wynika, że pęknięcia są wszędzie, pęknięcia są największe i pęknięcia są wszędzie.
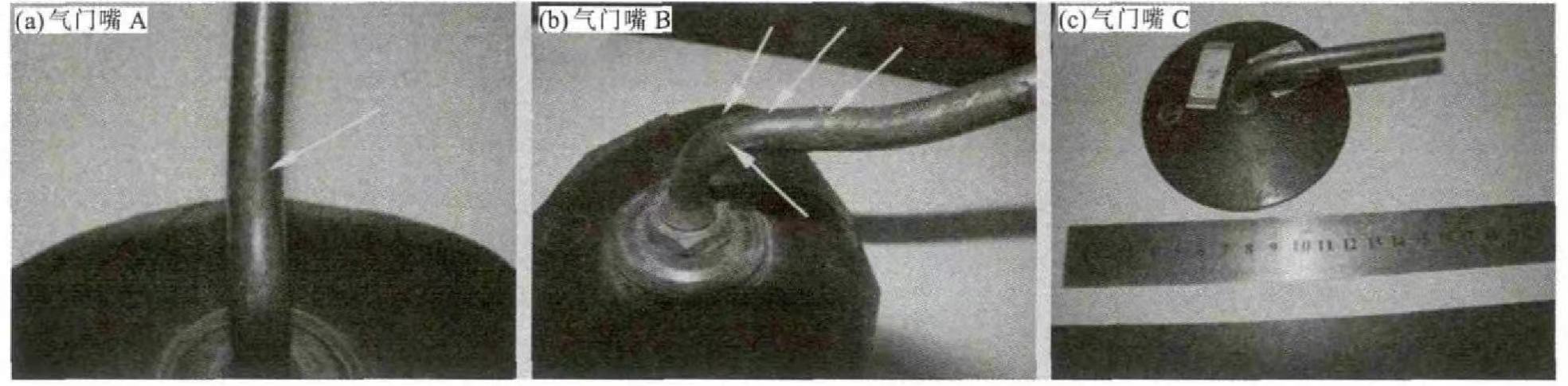
Częśćzawór oponyPróbki A, B i C zostały wycięte z zagięcia, a morfologia powierzchni została zaobserwowana za pomocą skaningowego mikroskopu elektronowego ZEISS-SUPRA55, a skład mikroobszaru został przeanalizowany za pomocą EDS. Rysunek 2 (a) przedstawia mikrostrukturę powierzchni zaworu B. Można zauważyć, że na powierzchni znajduje się wiele białych i jasnych cząstek (oznaczonych białymi strzałkami na rysunku), a analiza EDS białych cząstek wykazuje wysoką zawartość S. Wyniki analizy widma energetycznego białych cząstek pokazano na rysunku 2 (b).
Rysunki 2 (c) i (e) przedstawiają mikrostruktury powierzchni zaworu B. Z rysunku 2 (c) wynika, że powierzchnia jest niemal całkowicie pokryta produktami korozji, a elementy korozyjne produktów korozji według analizy widma energetycznego obejmują głównie S, Cl i O, zawartość S w poszczególnych pozycjach jest wyższa, a wyniki analizy widma energetycznego przedstawiono na rys. 2 (d). Z rysunku 2 (e) wynika, że na powierzchni zaworu A występują mikropęknięcia wzdłuż pierścienia zaworu. Rysunki 2 (f) i (g) przedstawiają mikromorfologie powierzchni zaworu C, powierzchnia jest również całkowicie pokryta produktami korozji, a elementy korozyjne obejmują również S, Cl i O, podobnie jak na rys. 2 (e). Przyczyną pękania może być pękanie korozyjne naprężeniowe (SCC) z analizy produktów korozji na powierzchni zaworu. Rys. 2(h) przedstawia również mikrostrukturę powierzchni zaworu C. Widać, że powierzchnia jest stosunkowo czysta, a skład chemiczny powierzchni analizowanej przez EDS jest podobny do składu stopu miedzi, co wskazuje, że zawór nie jest skorodowany. Porównując mikroskopową morfologię i skład chemiczny trzech powierzchni zaworu, wykazano, że w otaczającym środowisku znajdują się media korozyjne, takie jak S, O i Cl.
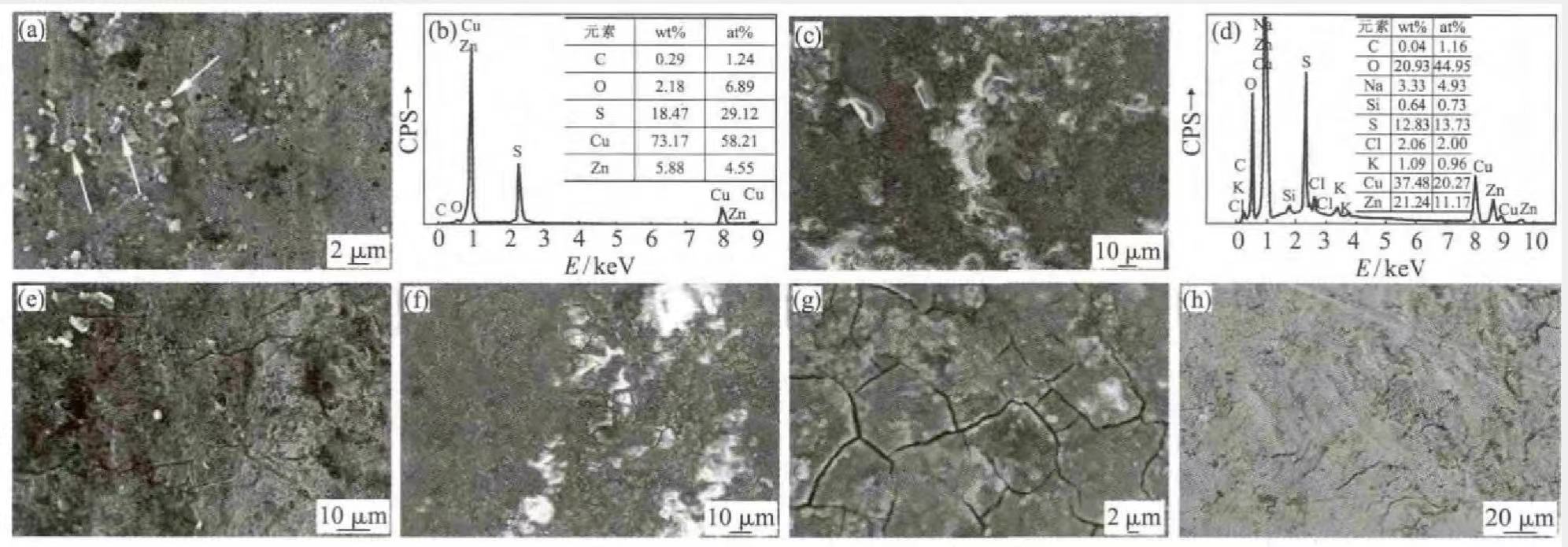
Pęknięcie zaworu B zostało otwarte podczas testu zginania i stwierdzono, że pęknięcie nie przebiło całego przekroju zaworu, pękło po stronie wygięcia wstecznego i nie pękło po stronie przeciwnej do wygięcia wstecznego zaworu. Wizualna kontrola pęknięcia pokazuje, że kolor pęknięcia jest ciemny, co wskazuje, że pęknięcie zostało skorodowane, a niektóre części pęknięcia są ciemne, co wskazuje, że korozja jest poważniejsza w tych częściach. Pęknięcie zaworu B zostało zaobserwowane pod skaningowym mikroskopem elektronowym, jak pokazano na rysunku 3. Rysunek 3 (a) przedstawia makroskopowy wygląd pęknięcia zaworu B. Można zauważyć, że zewnętrzne pęknięcie w pobliżu zaworu zostało pokryte produktami korozji, co ponownie wskazuje na obecność mediów korozyjnych w otaczającym środowisku. Zgodnie z analizą widma energetycznego, składnikami chemicznymi produktu korozji są głównie S, Cl i O, a zawartość S i O jest stosunkowo wysoka, jak pokazano na rysunku 3 (b). Obserwując powierzchnię pęknięcia, stwierdzono, że wzór wzrostu pęknięcia jest wzdłuż typu kryształu. Dużą liczbę pęknięć wtórnych można również zobaczyć, obserwując pęknięcie przy większych powiększeniach, jak pokazano na rysunku 3(c). Pęknięcia wtórne są oznaczone białymi strzałkami na rysunku. Produkty korozji i wzory wzrostu pęknięć na powierzchni pęknięcia ponownie pokazują cechy pęknięć korozyjnych naprężeniowych.
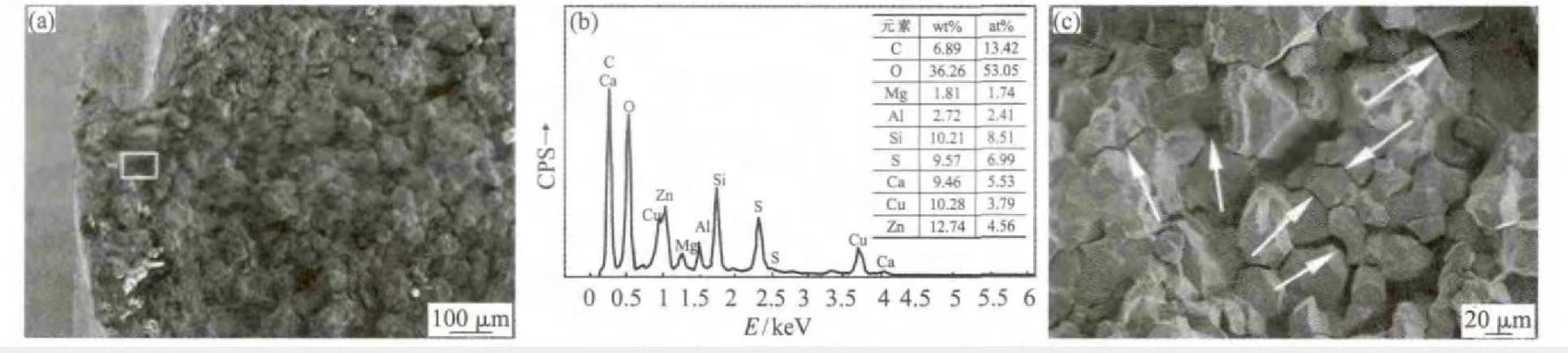
Pęknięcie zastawki A nie zostało otwarte, usuń część zastawki (w tym pękniętą pozycję), zeszlifuj i wypoleruj osiową część zastawki i użyj roztworu Fe Cl3 (5 g) +HCl (50 ml) + C2H5OH (100 ml), który został wytrawiony, a struktura metalograficzna i morfologia wzrostu pęknięcia zostały zaobserwowane za pomocą mikroskopu optycznego Zeiss Axio Observer A1m. Rysunek 4 (a) przedstawia strukturę metalograficzną zastawki, która jest strukturą dwufazową α+β, a β jest stosunkowo drobny i ziarnisty oraz rozłożony na matrycy fazy α. Wzory propagacji pęknięć na pęknięciach obwodowych pokazano na rysunku 4 (a), (b). Ponieważ powierzchnie pęknięć są wypełnione produktami korozji, szczelina między dwiema powierzchniami pęknięć jest szeroka i trudno jest odróżnić wzory propagacji pęknięć. zjawisko bifurkacji. Wiele wtórnych pęknięć (oznaczonych białymi strzałkami na rysunku) zaobserwowano również na tym pierwotnym pęknięciu, patrz rys. 4(c), a te wtórne pęknięcia rozprzestrzeniały się wzdłuż włókien. Wytrawioną próbkę zaworu obserwowano za pomocą SEM i stwierdzono, że było wiele mikropęknięć w innych pozycjach równolegle do głównego pęknięcia. Te mikropęknięcia miały swój początek na powierzchni i rozprzestrzeniły się do wnętrza zaworu. Pęknięcia miały rozwidlenie i rozciągały się wzdłuż włókien, patrz rys. 4 (c), (d). Środowisko i stan naprężenia tych mikropęknięć są prawie takie same jak w przypadku głównego pęknięcia, więc można wnioskować, że forma rozprzestrzeniania się głównego pęknięcia jest również międzykrystaliczna, co potwierdza również obserwacja pęknięcia zaworu B. Zjawisko rozwidlenia pęknięcia ponownie pokazuje charakterystykę pękania korozyjnego naprężeniowego zaworu.
2. Analiza i dyskusja
Podsumowując, można wnioskować, że uszkodzenie zaworu jest spowodowane korozją naprężeniową spowodowaną przez SO2. Pękanie korozyjne naprężeniowe musi na ogół spełniać trzy warunki: (1) materiały wrażliwe na korozję naprężeniową; (2) środowisko korozyjne wrażliwe na stopy miedzi; (3) określone warunki naprężenia.
Powszechnie uważa się, że czyste metale nie cierpią na korozję naprężeniową, a wszystkie stopy są podatne na korozję naprężeniową w różnym stopniu. W przypadku materiałów mosiężnych powszechnie uważa się, że struktura dwufazowa ma większą podatność na korozję naprężeniową niż struktura jednofazowa. W literaturze donoszono, że gdy zawartość Zn w materiale mosiężnym przekracza 20%, ma on większą podatność na korozję naprężeniową, a im wyższa zawartość Zn, tym wyższa podatność na korozję naprężeniową. Struktura metalograficzna dyszy gazowej w tym przypadku jest stopem dwufazowym α+β, a zawartość Zn wynosi około 35%, znacznie przekraczając 20%, więc ma wysoką wrażliwość na korozję naprężeniową i spełnia warunki materiałowe wymagane do pękania korozyjnego naprężeniowego.
W przypadku materiałów mosiężnych, jeśli wyżarzanie odprężające nie zostanie wykonane po odkształceniu na zimno, korozja naprężeniowa wystąpi w odpowiednich warunkach naprężenia i środowiskach korozyjnych. Naprężenie powodujące pękanie korozyjne naprężeniowe jest na ogół lokalnym naprężeniem rozciągającym, które może być naprężeniem przyłożonym lub naprężeniem szczątkowym. Po napompowaniu opony ciężarówki naprężenie rozciągające zostanie wygenerowane wzdłuż kierunku osiowego dyszy powietrza z powodu wysokiego ciśnienia w oponie, co spowoduje pęknięcia obwodowe w dyszy powietrza. Naprężenie rozciągające spowodowane wewnętrznym ciśnieniem opony można łatwo obliczyć zgodnie z σ=p R/2t (gdzie p jest ciśnieniem wewnętrznym opony, R jest średnicą wewnętrzną zaworu, a t jest grubością ścianki zaworu). Jednak ogólnie rzecz biorąc, naprężenie rozciągające generowane przez ciśnienie wewnętrzne opony nie jest zbyt duże i należy wziąć pod uwagę wpływ naprężenia szczątkowego. Miejsca pęknięć dysz gazowych znajdują się przy wygięciu do tyłu i jest oczywiste, że odkształcenie resztkowe przy wygięciu do tyłu jest duże i występuje tam resztkowe naprężenie rozciągające. W rzeczywistości w wielu praktycznych komponentach ze stopu miedzi pękanie korozyjne naprężeniowe rzadko jest spowodowane naprężeniami projektowymi, a większość z nich jest spowodowana naprężeniami resztkowymi, których nie widać i które są ignorowane. W tym przypadku przy wygięciu do tyłu zaworu kierunek naprężenia rozciągającego generowanego przez ciśnienie wewnętrzne opony jest zgodny z kierunkiem naprężenia resztkowego, a superpozycja tych dwóch naprężeń zapewnia warunek naprężenia dla SCC.
3. Wnioski i sugestie
Wniosek:
Pękaniezawór oponyjest głównie spowodowane korozją naprężeniową wywołaną przez SO2.
Sugestia
(1) Zlokalizuj źródło ośrodka korozyjnego w otoczeniuzawór oponyi staraj się unikać bezpośredniego kontaktu z otaczającym medium korozyjnym. Na przykład, warstwa powłoki antykorozyjnej może być nałożona na powierzchnię zaworu.
(2) Pozostałościowe naprężenie rozciągające powstające podczas obróbki plastycznej na zimno można wyeliminować za pomocą odpowiednich procesów, np. wyżarzania odprężającego po gięciu.
Czas publikacji: 23-09-2022