1. Test teoretyczny i analiza
Z 3zawory do oponpróbki dostarczone przez firmę, 2 to zawory, a 1 to zawór, który nie był jeszcze używany.W przypadku A i B zawór, który nie był używany, jest oznaczony kolorem szarym.Szczegółowy rysunek 1. Zewnętrzna powierzchnia zaworu A jest płytka, zewnętrzna powierzchnia zaworu B jest powierzchnią, zewnętrzna powierzchnia zaworu C jest powierzchnią, a zewnętrzna powierzchnia zaworu C jest powierzchnią.Zawory A i B są pokryte produktami korozji.Zawory A i B są popękane na zagięciach, zewnętrzna część zagięcia przebiega wzdłuż zaworu, wylot pierścienia zaworu B jest pęknięty w kierunku końca, a pomiędzy popękanymi powierzchniami na powierzchni zaworu A zaznaczona jest biała strzałka .Z powyższego wynika, że pęknięcia są wszędzie, pęknięcia są największe i pęknięcia są wszędzie.
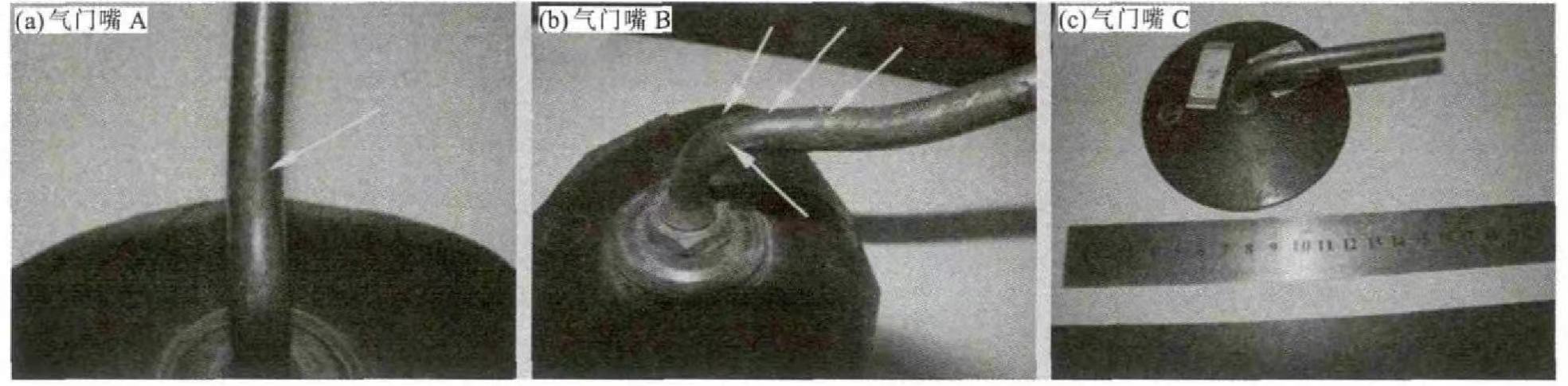
Częśćzawór oponyZ zagięcia wycięto próbki A, B i C, obserwowano morfologię powierzchni za pomocą skaningowego mikroskopu elektronowego ZEISS-SUPRA55 oraz analizowano skład mikroobszaru za pomocą EDS.Figura 2 (a) przedstawia mikrostrukturę powierzchni zaworu B.Można zauważyć, że na powierzchni znajduje się wiele białych i jasnych cząstek (oznaczonych białymi strzałkami na rysunku), a analiza EDS białych cząstek wykazuje wysoką zawartość S. Wyniki analizy widma energii białych cząstek pokazano na rysunku 2(b).
Rysunki 2 (c) i (e) przedstawiają mikrostrukturę powierzchni zaworu B. Z Rysunku 2 (c) można zobaczyć, że powierzchnia jest prawie całkowicie pokryta produktami korozji, a korozyjne elementy produktów korozji metodą analizy widma energii obejmują głównie S, Cl i O, zawartość S w poszczególnych pozycjach jest większa, a wyniki analizy widma energii przedstawiono na rys. 2(d).Na Rysunku 2(e) widać mikropęknięcia wzdłuż pierścienia zaworowego na powierzchni zaworu A. Rysunki 2(f) i (g) przedstawiają mikromorfologię powierzchni zaworu C, powierzchnia jest również całkowicie pokryte produktami korozji, a pierwiastki korozyjne obejmują również S, Cl i O, podobnie jak na rysunku 2 (e).Przyczyną pęknięć może być pękanie korozyjne naprężeniowe (SCC), które wynika z analizy produktów korozji na powierzchni zaworu.Na rys. 2(h) przedstawiono także mikrostrukturę powierzchni zaworu C. Można zauważyć, że powierzchnia jest stosunkowo czysta, a skład chemiczny powierzchni analizowanej metodą EDS jest podobny do składu stopu miedzi, co wskazuje, że zawór jest nie skorodowany.Porównując mikroskopową morfologię i skład chemiczny trzech powierzchni zaworów, wykazano, że w otaczającym środowisku występują czynniki korozyjne, takie jak S, O i Cl.
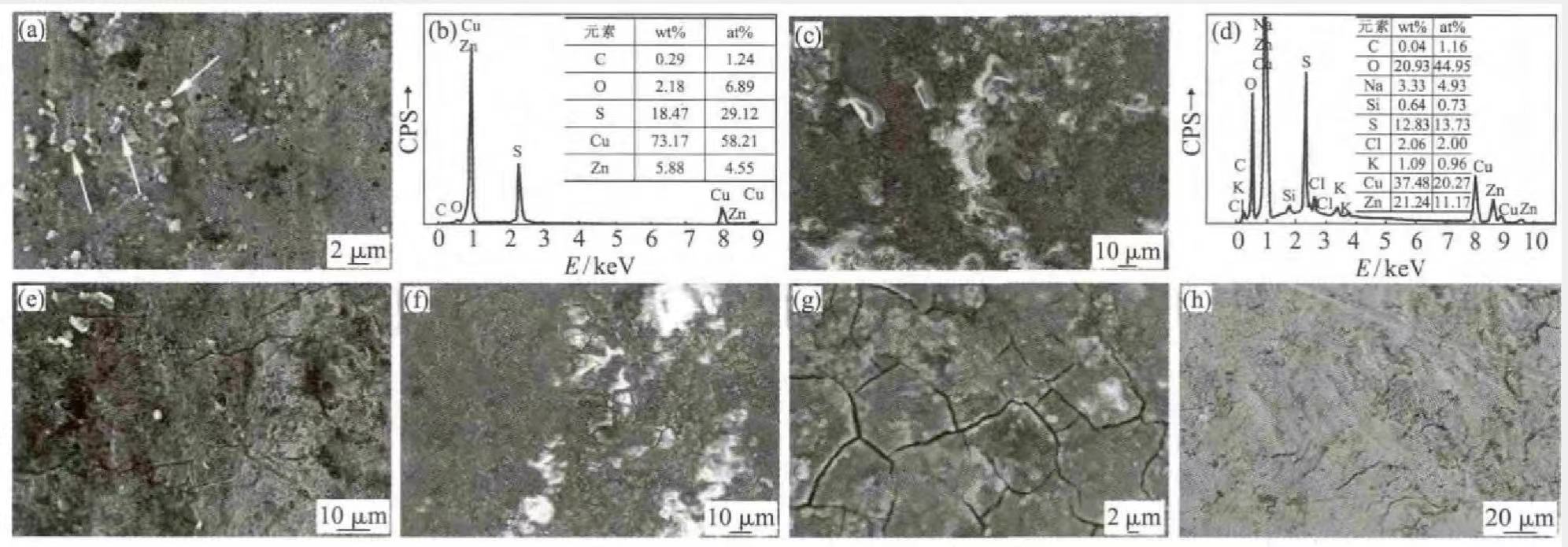
Pęknięcie zaworu B zostało otwarte poprzez próbę zginania i stwierdzono, że pęknięcie nie przechodziło przez cały przekrój zaworu, pękało po stronie zagięcia i nie pękało po stronie przeciwnej do zagięcia zaworu.Wizualna kontrola pęknięcia wykazuje, że kolor pęknięcia jest ciemny, co wskazuje, że pęknięcie zostało skorodowane, a niektóre części pęknięcia są ciemne, co wskazuje, że korozja w tych częściach jest poważniejsza.Pęknięcie zastawki B zaobserwowano pod skaningowym mikroskopem elektronowym, jak pokazano na ryc. 3. Ryc. 3 (a) przedstawia makroskopowy wygląd pęknięcia zastawki B.Można zauważyć, że zewnętrzne pęknięcie w pobliżu zaworu zostało pokryte produktami korozji, co ponownie wskazuje na obecność czynników korozyjnych w otaczającym środowisku.Według analizy widma energii składnikami chemicznymi produktu korozji są głównie S, Cl i O, a zawartość S i O jest stosunkowo wysoka, jak pokazano na rys. 3 (b).Obserwując powierzchnię pęknięcia, stwierdzono, że wzór wzrostu pęknięć przebiega wzdłuż typu kryształu.Obserwując pęknięcie przy większym powiększeniu, można również dostrzec dużą liczbę pęknięć wtórnych, jak pokazano na rysunku 3(c).Pęknięcia wtórne zaznaczono na rysunku białymi strzałkami.Produkty korozji i wzory wzrostu pęknięć na powierzchni pęknięcia ponownie wykazują cechy pękania korozyjnego naprężeniowego.
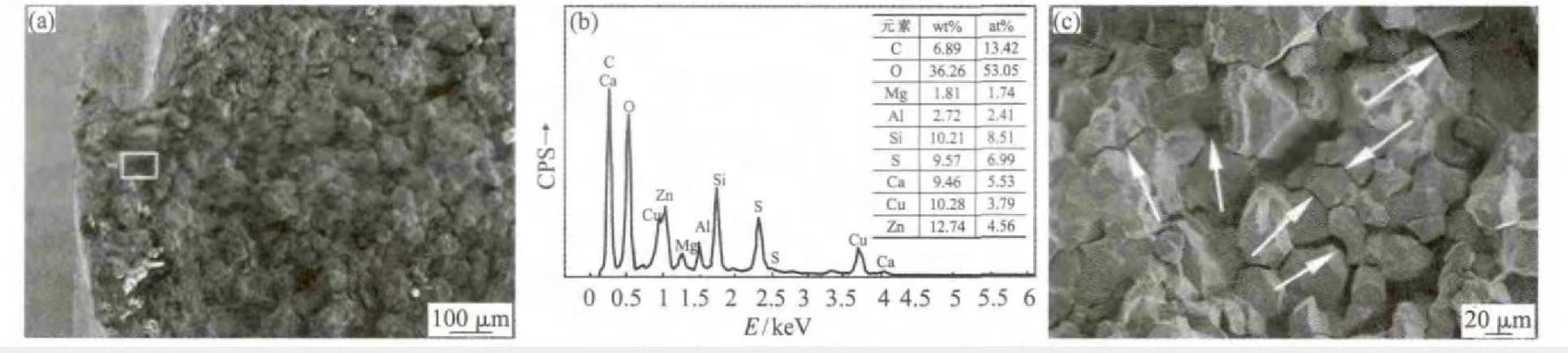
Pęknięcie zaworu A nie zostało otwarte, należy usunąć część zaworu (łącznie z pękniętą częścią), przeszlifować i wypolerować część osiową zaworu i użyć Fe Cl3 (5 g) +HCl (50 mL) + C2H5OH ( 100 mL) wytrawiono i obserwowano strukturę metalograficzną i morfologię wzrostu pęknięć za pomocą mikroskopu optycznego Zeiss Axio Observer A1m.Rysunek 4 (a) przedstawia strukturę metalograficzną zaworu, która jest strukturą dwufazową α+β, przy czym β jest stosunkowo drobne i ziarniste oraz rozmieszczone na matrycy fazy α.Schematy propagacji pęknięć na pęknięciach obwodowych pokazano na rys. 4 (a), (b).Ponieważ powierzchnie pęknięć są wypełnione produktami korozji, szczelina pomiędzy dwiema powierzchniami pęknięć jest szeroka i trudno jest rozróżnić wzorce propagacji pęknięć.zjawisko bifurkacji.Na tym pierwotnym pęknięciu zaobserwowano również wiele wtórnych pęknięć (oznaczonych białymi strzałkami na rysunku), patrz ryc. 4(c), a te wtórne pęknięcia rozprzestrzeniały się wzdłuż włókien.Wytrawioną próbkę zaworu poddano obserwacji metodą SEM i stwierdzono, że występowało wiele mikropęknięć w innych miejscach, równolegle do głównego pęknięcia.Te mikropęknięcia powstały na powierzchni i rozszerzyły się do wnętrza zaworu.Pęknięcia rozwidlały się i rozciągały wzdłuż włókien, patrz ryc. 4 (c), (d).Środowisko i stan naprężeń tych mikropęknięć są prawie takie same jak w pęknięciu głównym, stąd można wnioskować, że forma propagacji pęknięcia głównego jest również międzykrystaliczna, co potwierdza także obserwacja pęknięcia zaworu B. Zjawisko bifurkacji pęknięcie ponownie wykazuje cechy pękania korozyjnego naprężeniowego zaworu.
2. Analiza i dyskusja
Reasumując można stwierdzić, że przyczyną uszkodzenia zaworu jest pękanie korozyjne naprężeniowe wywołane SO2.Pękanie korozyjne naprężeniowe zazwyczaj musi spełniać trzy warunki: (1) materiały wrażliwe na korozję naprężeniową;(2) środowisko korozyjne wrażliwe na stopy miedzi;(3) określone warunki stresowe.
Powszechnie uważa się, że czyste metale nie ulegają korozji naprężeniowej, a wszystkie stopy są podatne na korozję naprężeniową w różnym stopniu.W przypadku materiałów mosiężnych ogólnie uważa się, że struktura dwufazowa ma większą podatność na korozję naprężeniową niż struktura jednofazowa.W literaturze donoszono, że gdy zawartość Zn w materiale mosiężnym przekracza 20%, ma on większą podatność na korozję naprężeniową, a im wyższa zawartość Zn, tym większa podatność na korozję naprężeniową.Struktura metalograficzna dyszy gazowej w tym przypadku jest stopem dwufazowym α+β, a zawartość Zn wynosi około 35%, znacznie przekraczając 20%, dzięki czemu charakteryzuje się dużą wrażliwością na korozję naprężeniową i spełnia warunki materiałowe wymagane do naprężeń pękanie korozyjne.
W przypadku materiałów mosiężnych, jeśli po odkształceniu podczas pracy na zimno nie zostanie przeprowadzone wyżarzanie odprężające, w odpowiednich warunkach naprężenia i w środowisku korozyjnym wystąpi korozja naprężeniowa.Naprężenie powodujące pękanie korozyjne naprężeniowe to zazwyczaj lokalne naprężenie rozciągające, które może być naprężeniem przyłożonym lub naprężeniem szczątkowym.Po napompowaniu opony ciężarówki w kierunku osiowym dyszy powietrznej powstaną naprężenia rozciągające, spowodowane wysokim ciśnieniem w oponie, co spowoduje pęknięcia obwodowe dyszy powietrznej.Naprężenie rozciągające wywołane ciśnieniem wewnętrznym opony można w prosty sposób obliczyć ze wzoru σ=p R/2t (gdzie p to ciśnienie wewnętrzne w oponie, R to wewnętrzna średnica zaworu, a t to grubość ścianki opony). zawór).Jednakże, ogólnie rzecz biorąc, naprężenie rozciągające generowane przez ciśnienie wewnętrzne opony nie jest zbyt duże i należy wziąć pod uwagę wpływ naprężeń szczątkowych.Wszystkie miejsca pęknięć dysz gazowych znajdują się na tylnym zagięciu i oczywiste jest, że szczątkowe odkształcenie na tylnym zagięciu jest duże i występuje tam szczątkowe naprężenie rozciągające.W rzeczywistości w wielu praktycznych elementach ze stopów miedzi pękanie korozyjne naprężeniowe rzadko jest spowodowane naprężeniami projektowymi, a większość z nich jest spowodowana naprężeniami szczątkowymi, które nie są widoczne i ignorowane.W tym przypadku na tylnym zagięciu zaworu kierunek naprężeń rozciągających wytwarzanych przez ciśnienie wewnętrzne opony jest zgodny z kierunkiem naprężeń szczątkowych, a superpozycja tych dwóch naprężeń stanowi warunek naprężenia dla SCC .
3. Wnioski i sugestie
Wniosek:
Pękaniezawór oponyjest spowodowane głównie pękaniem korozyjnym naprężeniowym powodowanym przez SO2.
Sugestia
(1) Znajdź źródło czynnika korozyjnego w otoczeniuzawór oponyi staraj się unikać bezpośredniego kontaktu z otaczającym czynnikiem korozyjnym.Na przykład na powierzchnię zaworu można nałożyć warstwę powłoki antykorozyjnej.
(2) Szczątkowe naprężenia rozciągające powstałe podczas obróbki na zimno można wyeliminować za pomocą odpowiednich procesów, takich jak wyżarzanie odprężające po zginaniu.
Czas publikacji: 23 września 2022 r